Our TAKUMI Machining Centers are equipped with the latest Heidenhain TNC control 640.
CNC-MaschinesGraphite, G-Series
The graphite artist
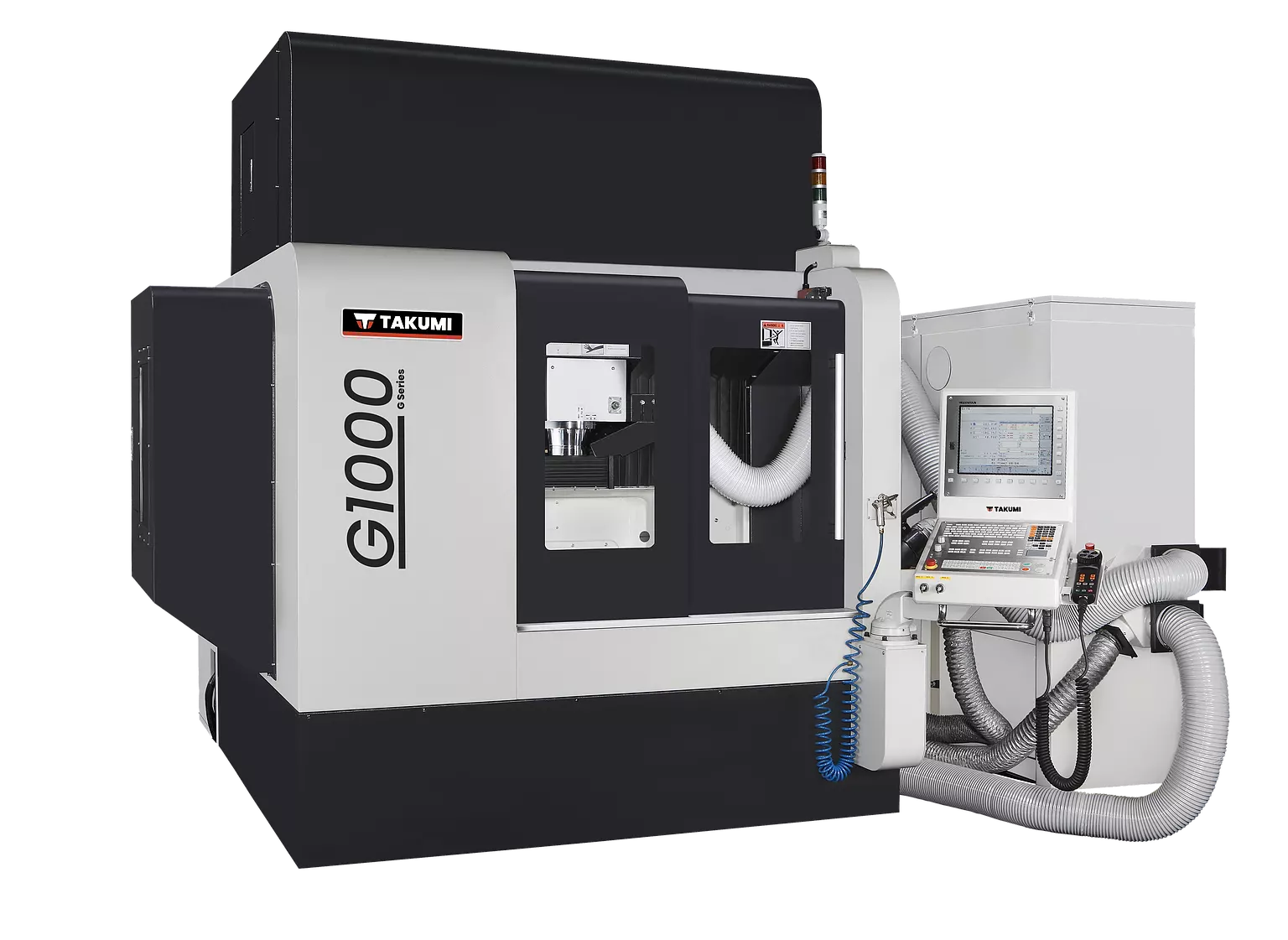
TAKUMI G 1000
The G 1000 is the ideal CNC machine for your production if you are looking for a steadfast solution for graphite machining with an optimal price-performance ratio. The machining center is equipped with first-class components as standard and can also be expanded with numerous additional options - for the production of workpieces with the finest contours specifically according to the requirements of your production.
Travels and Table
X-Axis (mm): 1.020
Y-Axis (mm): 700
Z-Axis (mm): 500
Table working surface W x D (mm): 1.050 x 700
Spindle Speed (rpm): 25.000
Produkt anfragen
Y-Axis (mm): 700
Z-Axis (mm): 500
Table working surface W x D (mm): 1.050 x 700
Spindle Speed (rpm): 25.000
- Completely enclosed machining area incl. extraction for modern graphite machining.
- High form and dimensional accuracy due to compact gantry design
- Comprehensive basic equipment for a first-class price/performance ratio
- Stable and rigid gantry construction with high temperature resistance
- Absolute direct travel measuring system
- System for compensation of thermal spindle expansion
- Cooling system for the ball screw - 25,000 min-1, HSK-E50, motor spindle Graphite extraction system"
Details
Specifications - G 1000
Travels | |
---|---|
X-Axis (mm) | 1.020 |
Y-Axis (mm) | 700 |
Z-Axis (mm) | 500 |
Table | |
---|---|
Table working surface W x D (mm) | 1.050 x 700 |
Load max. (uniform distribution) (kg) | 800 |
Distance from spindle nose to table (mm) | 180 - 680 |
Distance between columns (mm) | 1.080 |
T-Slots (DIN 650) | 6 x 18 x 125 |
Spindle | |
---|---|
Spindle Taper | HSK50-E |
Type | Motorspindel |
Power S1/S6 (kW) | 20 / 26 |
Torque S1/S6 (Nm) | 10,4 / 13,5 |
Spindle Speed (rpm) | 25.000 |
Feed Rate | |
---|---|
Rapid Traverse X/Y/Z-Axis (m/min) | 30 / 30 / 30 |
Cutting Feed Rate X/Y/Z-Axis (mm/min) | 20 |
ATC & Magazine | |
---|---|
ATC Type | Doppelgreifer |
Magazine Capacity | 30 |
Maximum Tool Diameter (mm) full / next pocket empty | 75 |
With Empty Pockets (mm) | 120 |
Maximum Tool Length (mm) | 300 |
Maximum Tool Weight (kg) | 7 |
Space & System Requirements | |
---|---|
Maximum Floor Space (mm) W x L x H | 3.950 x 4.600 x 2.950 |
Machine Net Weight (kg) | 9.100 |
Electrical Power Consumption (kVA / A) | 50 / 125 |
Air Requirements (bar) | 6 |
Spindle
Choose the spindle that suits you
Spindle options | G 1000 |
---|---|
Drehzahl max. (1/min) | 25.000 |
Leistung S1/S6 (kW) | 20 / 26 |
Drehmoment S1/S6 (Nm) | 10,4 / 13,5 |
Schnittstelle | HSK50-E |
Standard / Optional | Standard |
Features
Always perfectly equipped
Great features of our standard equipment
- Heidenhain iTNC 640 Control
- Graphite collector
- Linear Scales
- 15,000 RPM, CAT/BT40, inline spindle
- Spindle thermal compensation system
- Chip flushing
- Spindle cooling
- Full enclosure
- Ethernet interface
- 30T arm type ATC (G1000)
With further optional equipment you can adapt the TAKUMI G 1000 to your needs
- Ballscrew cooling system
- Part probe measurement system
- Touch probe for tool measurement
- Manual pulse generator (MPG)
- Programmable airblow machining
- Programmable airblow through spindle machining
Highlights
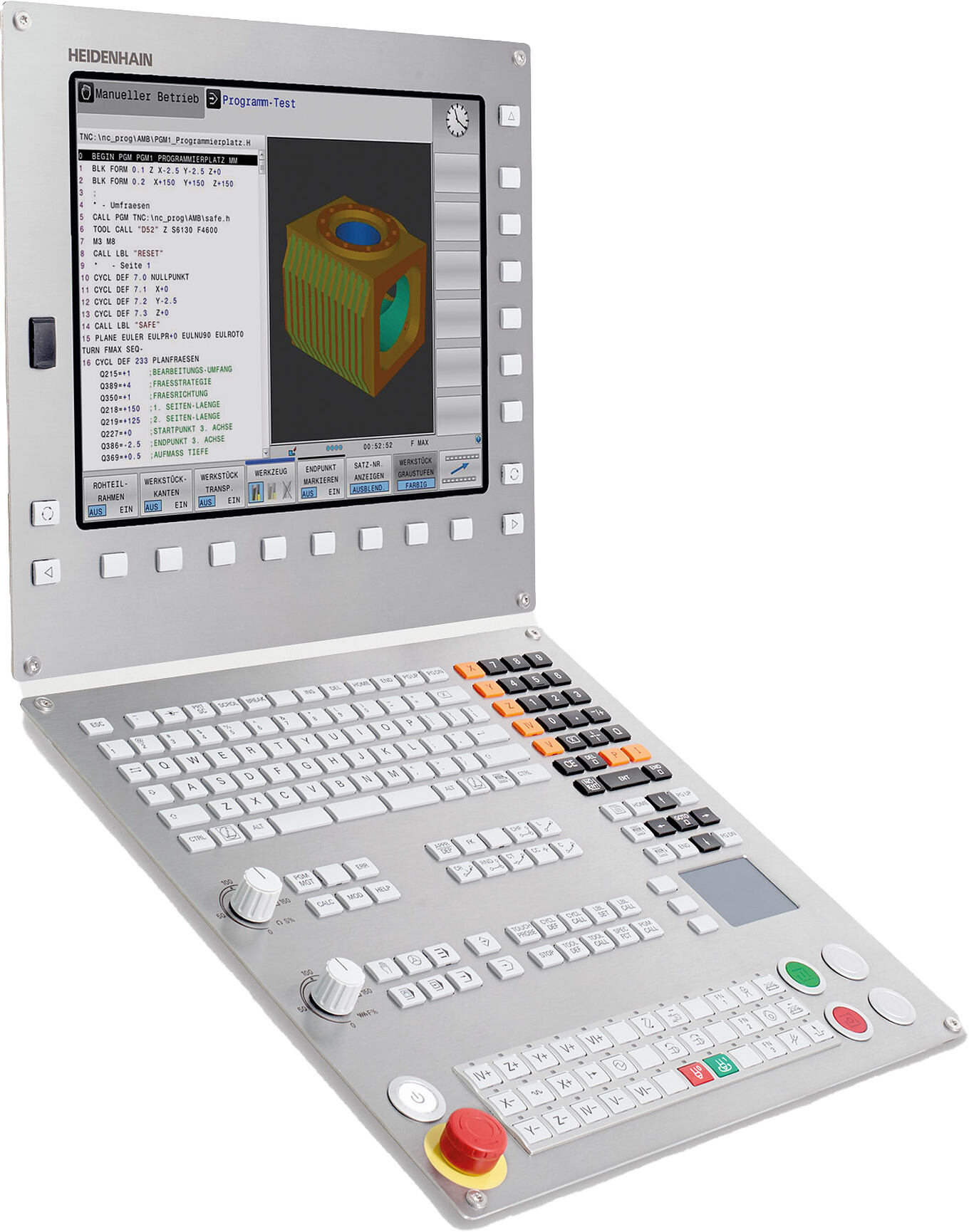
Heidenhain Control TNC 640
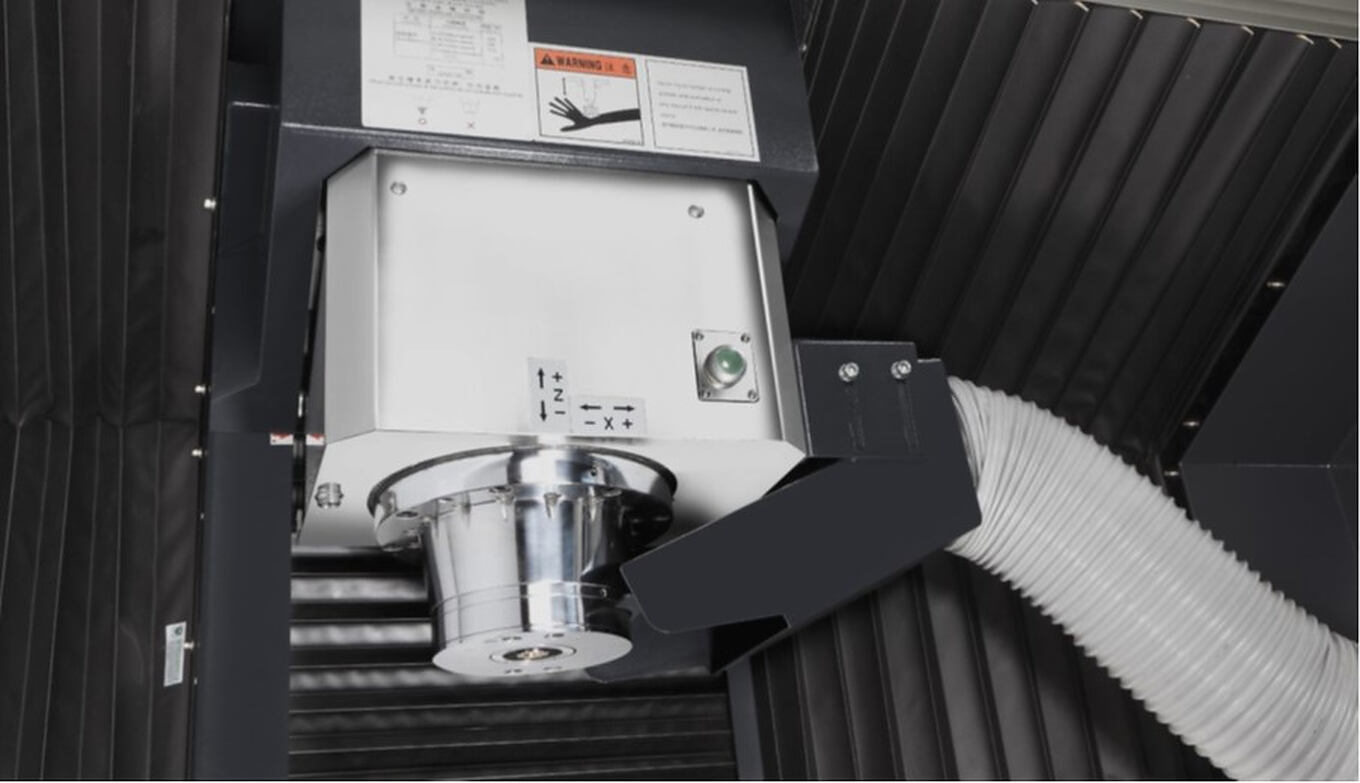
Extraction unit
- Fully-enclosed covers make sure a safe, clean and healthy working environment and effectively reduce graphite particles contamination to its minimum.
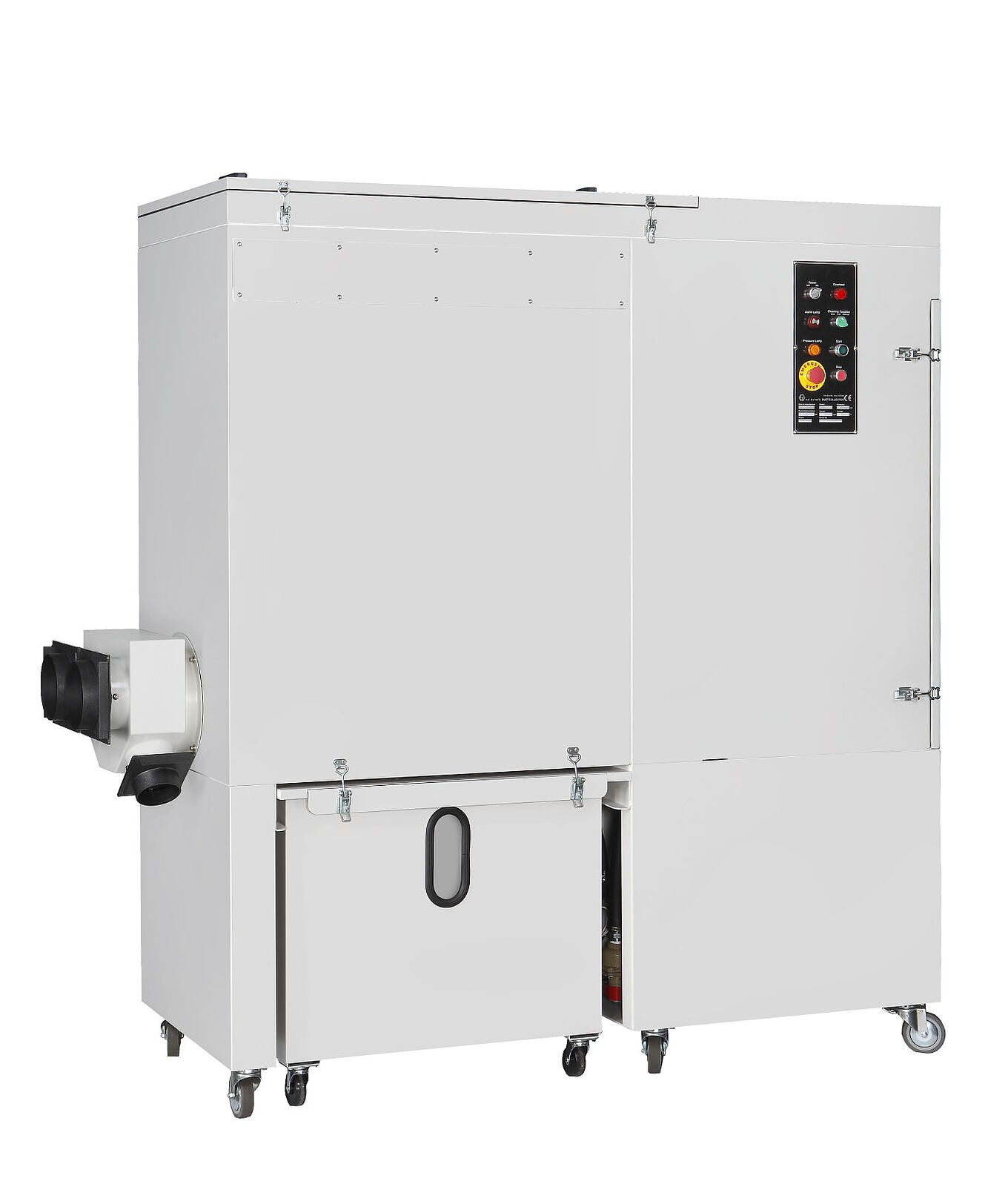
Vaccum system on the headstock
- The particle-collection nozzle keeps a distance at 150mm to the tool tip which not only makes the particle-collection rate above 83%,but also avoids from the motion conflict.